沿革
- 会社の歴史
- 技術の歴史
1968-2000第一ステージ ゼロからのものづくり
1968年、古屋昌則が株式会社フルヤ金属を設立し、その後、工業用貴金属事業に参入しました。そして、苦難の末、1981年には国内初のイリジウムルツボの製造に成功。つくば工場の新設などを通じ、取り扱いの難しい貴金属であるイリジウムとルテニウムを取り扱うメーカーとしての基盤と技術力の礎を築きました。
1968
フルヤ金属設立
8月22日にフルヤ金属が設立されました。前身は古屋堯民の父である古屋昌則が、1951年3月に東京・三鷹台の自宅で創業した「古屋商店」でした。フルヤ金属を設立した当時は、宝飾用貴金属の販売が主な事業でした。
1975
工業用貴金属事業に参入
事業の中心を宝飾用から工業用貴金属に切り替えました。工場化した自宅の車庫がフルヤ金属のものづくりのスタート地点となりました。
1977
本社工場を三鷹台から高田一丁目に移転
事業の拡大に伴い、三鷹台の自宅の一角の本社工場を豊島区高田へ移転しました。新しい本社工場は倉庫として使われていた建物でした。
1981
国内初のイリジウムルツボ製造に成功
それまで海外メーカーしか取り扱っていなかったイリジウムルツボを当社が国内メーカーで初めて製造することに成功しました。
1982
工業用貴金属に特化 高田工場を新設
生産力の増強のため、豊島区高田に第2の工場である高田工場を新設。当時を知る社員からは親しみを込めて「高田馬場」と呼ばれています。
1983
三菱商事(株)と貴金属地金売買契約締結
信越化学工業(株)精密材料部の代理店販売開始
大学等の研究機関との取引実績を活かし、同社が手がけるPBN(Pyrolytic Boron Nitride、焼成窒化ボロン)ルツボの代理店販売を開始しました。
1989
新日本製鐵(株)、旭硝子(株)と溶銑・溶鋼・連続測温用温度計を共同開発
製鋼の過程で高炉内の温度をリアルタイムに連続して測ることができる温度計を、現 新日鐵住金(株)、現 AGC(株)と共同開発しました。従来、高炉内の温度を測るための温度計は炉内の高温に耐えられず、連続した測温ができませんでしたが、この溶銑・溶鋼・連続測温用温度計により、連続したリアルタイムの温度把握が可能となりました。
1990
つくば工場新設 本社工場および高田工場を集約化
高田の本社工場と高田工場を茨城県下館市(現 筑西市)に新設した「つくば工場」に集約。1970年代から80年代を支えた「高田馬場時代」が終焉を迎え、新しい時代の幕開けとなりました。
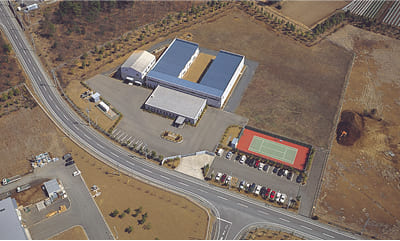
プラズマ溶解技術の開発
従来はセラミクスのルツボで金属を溶解する手法が行われてきましたが、このルツボから不純物が混入して溶融金属の純度が上がらない問題がありました。そこで、溶解の高純度化を実現するために、装置メーカーと協力して、セラミクスのルツボを使わないプラズマ溶解炉を開発し、設備を導入しました。

1991
航空宇宙技術研究所と高温用温度センサー
(イリジウム合金使用)を共同開発
高温用温度センサーは、科学技術庁(現 文部科学省)より産学官提携助成事業補助金を受けて共同開発を行ったものです。イリジウム熱電対で1,900℃レベルのガス温度を測定するというものでした。
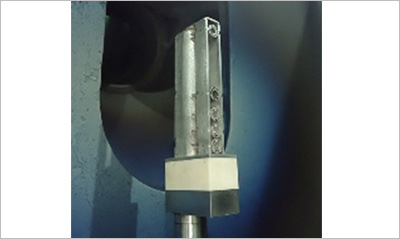
1993
ウエスタンプラチナム社から地金の直接仕入れを開始
南アフリカ共和国の鉱山会社であるウエスタンプラチナム社から貴金属地金を直接仕入れることにより、貴金属地金の安定調達を行うことが可能となりました。
1995
プラチナ精製において硝酸フリーシステムを実現
1980年代から行われていたプラチナの回収・精製は、プラチナを溶かす酸化剤として王水が必要でした。当社が実現した独自の手法は、王水を使わず、濃硝酸による環境への影響を防ぐとともに、溶解の効率化を可能としました。この時に得たノウハウが、後のイリジウムやルテニウムの精製に活かされました。
1997
イリジウム精製回収装置(イリジウムダイレクト溶解システム)開発・導入
イリジウムの精製は、最初の薬品に溶かす過程で非常に多くの時間と手間がかかる工程でした。当時はイリジウム化合物の需要が急増しており、対応に苦慮していました。そこで、従来の溶解工程とは全く異なる独自の溶解技術を考案し開発に成功しました。さらに、自動化設備を自社設計して導入し、需要に対応することが出来ました。現在では、鉱山会社以上のイリジウム精製キャパシティーを持つに至っています。
1998
つくば工場敷地内に「つくば研究開発センター」を開設
つくば研究開発センターは薄膜技術の研究開発を目的として開設されました。
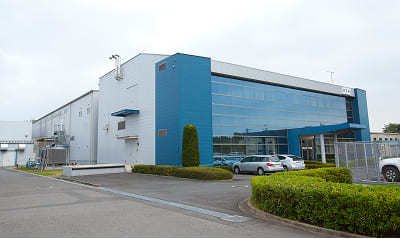
ウエハ熱電対開発
半導体の製造工程の1つである高温処理工程において必要となる温度センサーを開発しました。丸いウエハの表面の温度を測ることで装置内の温度を正確に確認することができます。
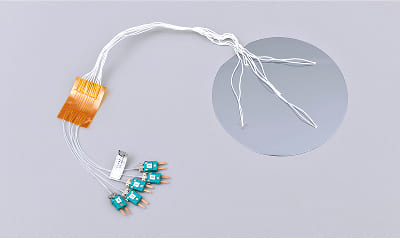
1999
APC素材開発
APCは、銀(Ag)とパラジウム(Pd)に銅(Cu)を加えた銀合金で、耐腐食性に優れています。APCは耐腐食性に優れた銀合金です。光ディスク(開発当初はCD-R用)は金を使用していましたが、APCは金よりも安価で腐食性に優れていたため、金の代替として使用が始まりました。現在もBlu-ray diskで使用されています。
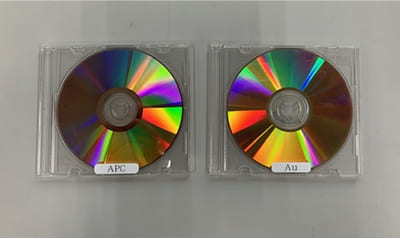
2000
つくば工場にて「ISO9001」取得
全製品の品質管理をより厳格に行うことを目的に国際品質保証規格であるISO9001の認証を取得しました。
PGM除去装置が完成
使用済みのイリジウムルツボから、高純度のイリジウムの精製ができるようになりました。
2001-2020第二ステージ 拡大への歩み
事業の拡大に合わせて土浦工場と千歳工場を新設し、高機能製品の研究開発に注力していきました。そして、JASDAQ上場を経て、「イリジウム・ルテニウムで世界一」を目指し、世界への挑戦を加速させました。高い世界シェア率を誇る製品を生み出すことにより、2014年と2020年の2度にわたってグローバルニッチトップ企業に選定されるなど、国際的な競争力を高めました。
2001
新合金FPOの開発
当社が独自に開発した酸化物分散型強化白金です。機能性ガラス製造に不可欠な白金器具の材料として当社の主力製品に位置付けられました。
2002
ルテニウム精製回収装置(ルテニウムダイレクト溶解システム)開発・導入
難溶解性でリサイクルの難しいルテニウムをシンプルな工程で、かつ高効率・高純度でリサイクル可能な新技術を開発しました。
研究開発部を設立
素材・センサー・薄膜材料・化学化合物・精製・回収と多岐にわたる研究を効果的に行うべく、素材、薄膜、ケミカルの3部門を持つ研究開発部を発足しました。全く異なる技術をもつ3部門ですが、この部門が互いの技術を共有することで新しい研究テーマの創出や技術課題の解決に役立っています。
2003
つくば工場敷地内に工場B棟を新設
ハードディスク向けルテニウムターゲットの製造設備を備えたB棟が完成しました。
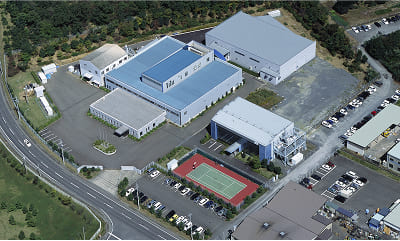
2004
ルテニウム精製本格化
当社のルテニウム精製は、つくば工場での石油化学向けの酸化触媒用のルテニウム化合物の製造を機に本格化しました。ルテニウム化合物製造のためにプレハブ小屋を建て、設備を運び入れて蒸留技術を磨き、ルテニウム精製の基本技術を確立しました。この時に確立されたルテニウム精製の技術は、2005年に完成するつくば工場C棟の10t/年の大型精製ラインに引き継がれました。
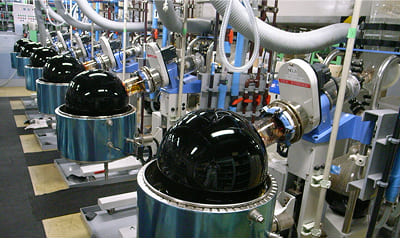
2005
つくば工場敷地内に工場C棟を新設
ルテニウム精製の需要の増加を見込み、PGMの回収リサイクルや化合物の開発が行われていた旧C棟を増築しました。
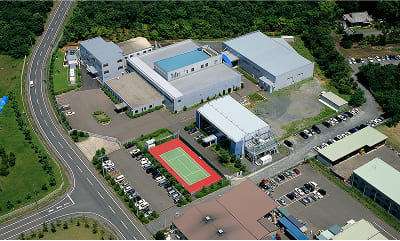
ロンドン・プラチナ・パラジウム・マーケット登録認証を取得
プラチナとパラジウム市場における国際的な登録認定機関であるロンドン・プラチナ・パラジウム・マーケット(LPPM)の技術審査に合格し、公認溶解業者(グッド・デリバリー)としての登録認証を取得しました。
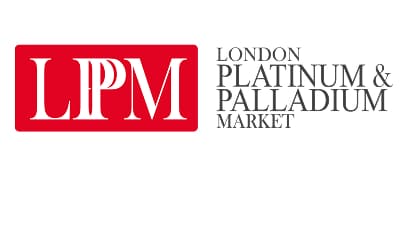
SPS1号機を導入
SPS(Spark Plasma Sintering、放電プラズマ焼結)は、粉末試料を急速加熱することにより、焼結体を短時間で緻密化できる技術です。つくば工場に焼結機1号機として導入されました。
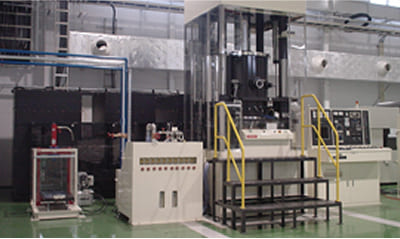
ルテニウムターゲットがハードディスク向けに量産採用となる
小型かつ軽量で大容量の記録を可能にするハードディスク(垂直磁気記録方式)向けルテニウムターゲットが量産採用されました。
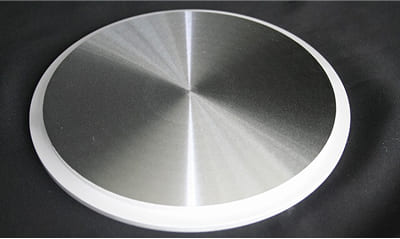
2006
つくば工場にて「ISO14001」取得
ケミカル部門への進出や薬品を扱う機会が増えたことから、環境へのリスクに対する取り組みを強化するために国際環境規格であるISO14001の認証を取得しました。
JASDAQ証券取引所に上場
9月27日、工業用貴金属専業メーカーとしては史上初の上場を果たしました。この時に「イリジウム・ルテニウムで世界一」のフレーズが生まれました。
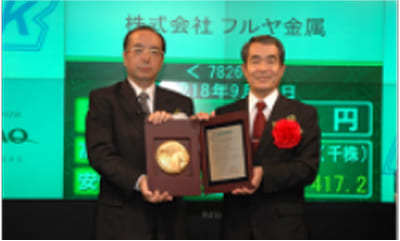
NEW-APCを開発
1999年に開発した当社オリジナルの銀合金「APC」の機能をさらに向上させたNEW-APCを開発しました。NEW-APCは、APCの持つ耐腐食性を維持しつつ、耐熱性を大幅に向上させ、さらに従来のAPCより高い反射率を有するという優れた特性を持っています。主に液晶や有機ELなどディスプレイ分野で使用されています。
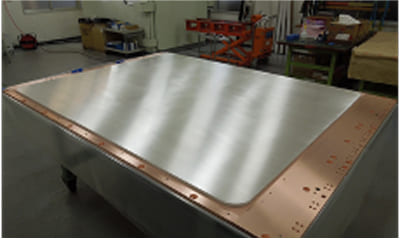
2007
つくば工場敷地内に工場D棟を新設
半導体製造装置用の温度センサー(熱電対)の生産増強と将来的なターゲットの生産増強を見込み、D棟が新設されました。
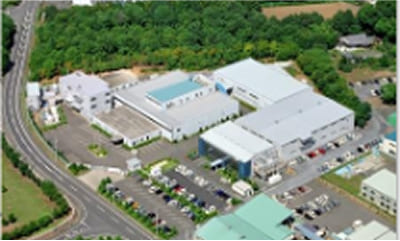
土浦工場を新設 工場棟を建設し貴金属回収精製ラインを増設
ルテニウム精製能力の増強を目的として、土浦工場を新設しました。土浦工場の新設によってルテニウム精製能力は、従来のおよそ2倍となり、当社は年間15~20tのルテニウムの精製が可能となりました。
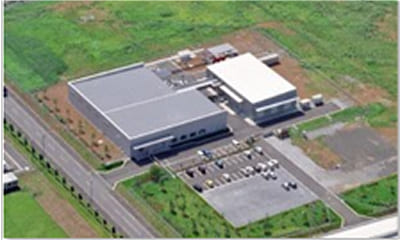
九州出張所開設
2008
新合金GS-FPOの開発
GS-FPOは、Grain Stabilized Furuya Platinum alloys with Oxide particles の略称で、2001年に開発されたFPOをさらに改良した、当社独自の高性能白金合金です。
1500℃の高温下でも横長な結晶粒形状を維持させることで、ガラス溶解用白金器具のロングライフ化を実現しました。
2009
土浦工場にて「ISO14001」取得
土浦工場で生産する製品の品質管理を厳格に行うことを目的に、つくば工場に続き国際品質保証規格であるISO14001の認証を取得しました。
つくば工場において計量法および国際規格「ISO17025」の要請に基づき校正事業者「JCSS」として登録JCSS国際MRA対応認定事業者として認定
国際標準の高い品質を提供するために、R熱電対の校正における国際MRA対応JCSS校正事業者の認定を取得しました。
2010
千歳工場を新設
半導体製造装置用の温度センサー(熱電対)の石英保護管を内製化するために千歳工場を新設しました。石英保護管の内製化は、かねてよりお客様から声が上がっており、それを実現するものでした。
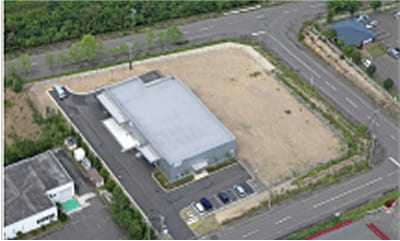
2011
田中貴金属工業(株)と資本業務提携契約を締結
貴金属国内最大手の田中貴金属工業(株)との間でイリジウム地金の安定供給等を目的として資本業務提携契約を締結しました。
韓国フルヤメタル設立
工業用貴金属製品の販売を行う、初の海外100%子会社として現地法人FURUYA METAL KOREA Co.,Ltd.を韓国ソウル市内に設立しました。半導体産業やスマートフォン市場において成長を遂げていた韓国企業への販売体制の強化となりました。
大型イリジウムルツボを(株)福田結晶技術研究所に納入
CZ法(チョクラルスキー法)による大型サファイア育成は、融点2,040℃と高温のため、高融点材であるイリジウムルツボを使用します。当時、世界最大のφ330のイリジウムルツボを作製し、大型結晶の育成と事業の立ち上げに貢献しました。
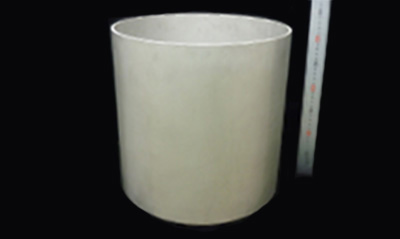
2013
米国フルヤメタル設立
第2の海外100%子会社としてアメリカ合衆国ニューハンプシャー州マンチェスター市にFURUYA METAL AMERICAS INC.を設立しました。アジアに次ぐ第2の輸出先である北米への現地法人の設立は、海外市場へのさらなる進出を支えました。
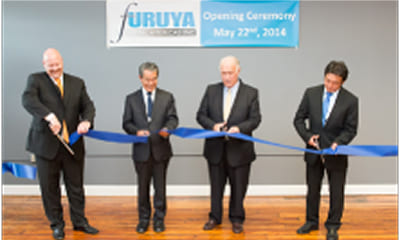
土浦工場敷地内に溶解炉棟を新設し乾式炉を導入
PGMのリサイクルを行う最新鋭の乾式炉を導入し、PGMの含有量が少ないスクラップからでも高効率でPGMが回収できる体制を強化しました。
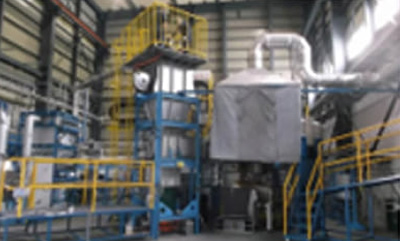
イリジウム-ロジウム合金熱電対販売開始
イリジウム-ロジウム合金熱電対は2,000℃を超える超高温を計測することができます。半導体やLED等の製造工程で高温を制御するのに最適です。
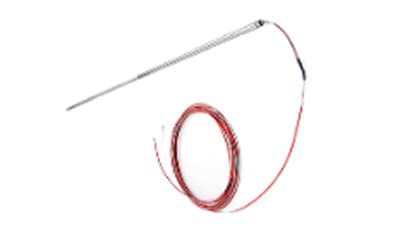
2014
FSW用イリジウム合金ツール販売
イリジウム合金の摩擦攪拌接合(Friction Stir Welding)ツールを世界で初めて製品化しました。
この製品はイリジウム合金を材料としており、融点が2,600℃以上の金属でも接合できる高温強度を持ちます。
当社のイリジウム合金ツールは、従来のFSWツールでは、融点が高すぎるために接合できなかったモリブデン(融点2,623℃)やチタンなどの金属の接合を可能にしました。
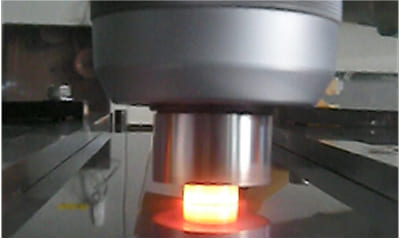
土浦工場敷地内に触媒棟新設
ルテニウム化合物から触媒を量産するために触媒棟を新設しました。2013年に導入した乾式炉と、この触媒棟の新設によって、高純度のPGMパウダーから化合物をつくり、触媒に加工して販売、さらに集荷した使用済みの触媒からPGMを回収・精製し、再び高純度PGMパウダーにする、高度なリサイクルモデルが完成しました。
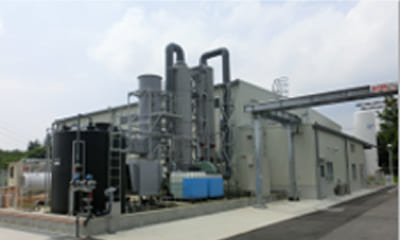
経済産業省認定グローバルニッチトップ企業100選に認定
工業用貴金属製品を専門とするメーカーとしては、唯一グローバルニッチトップ企業に選定されました。イリジウムルツボで6割強、ルテニウムターゲットで3割強の世界シェアを持つこと、さらに、加工が困難なPGMの原材料調達から精製・加工・リサイクルといった独自の技術を確立し、高品質な製品を提供する点が高い評価を受けました。
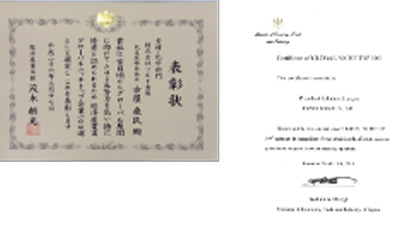
2015
「FT-eco触媒」の量産技術を確立
FT-eco触媒には青果物の腐敗を早めるエチレン(C2H4)を低温で効率的に分解する機能があります。従来の触媒でエチレンを効率良く分解するためには200℃以上の環境が必要でしたが、FT-eco触媒は氷点下から30℃の環境でも効率良くエチレンを水(H2O)と二酸化炭素(CO2)に分解することが可能な画期的な触媒です。
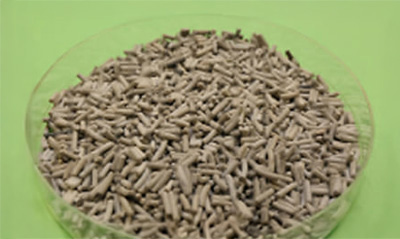
STT-RAM向け溶解ルテニウムターゲット開発
STT-RAM(次世代メモリの電極)に使用されるターゲット材は極めて高い純度が要求されます。当社が開発した溶解ルテニウムターゲットは99.999%(ファイブナイン)以上の純度を達成した極めて高純度のルテニウムターゲットです。
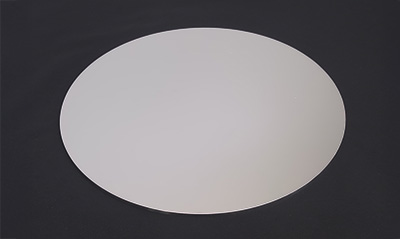
2016
R-SP(新強化型熱電対)販売開始
R-SPは従来の熱電対と比べ、約2倍の強度を持つ熱電対です。これにより高温域においても長寿命を実現しました。
R-SPの「R」はR熱電対の強化版を意味し、「SP」は金属組織の特徴を表すStripe Pattern(ストライプパターン)とSpecial(スペシャル)を掛けたものです。
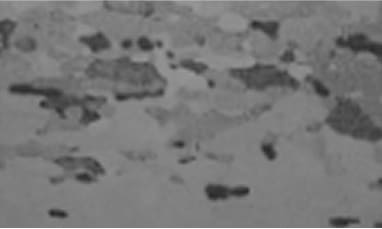
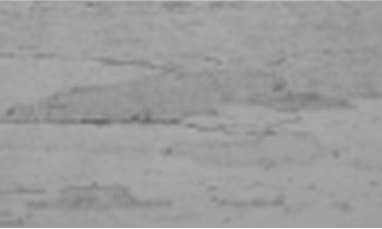
SPS4号機を導入
当時、次世代半導体向けターゲットとして、大型のルテニウムターゲットの需要が高まってきていました。そのため、大型品を製造できる大型SPS装置をSPS4号機として導入しました。
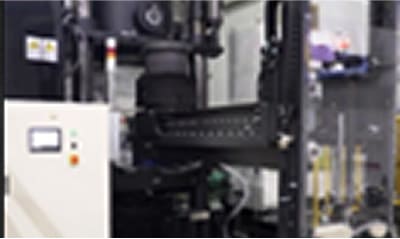
2019
固溶ナノ合金の量産化技術を確立
当社と京都大学の研究グループは、これまで安定的な量産が難しかったナノサイズの合金を効率的に作る新しい技術を共同開発しました。この技術では、1nmの非常に小さな粒子で均一な合金を作ることが可能になり、触媒としての性能が大幅に向上します。特に、排ガス浄化や化学プロセスに役立つ触媒の製造に応用されることが期待されています。従来の方法では手間がかかっていた合金触媒の作成が、一度の工程で効率的にできるようになり、今後は多くの分野での需要に応えることができる革新的な技術です。
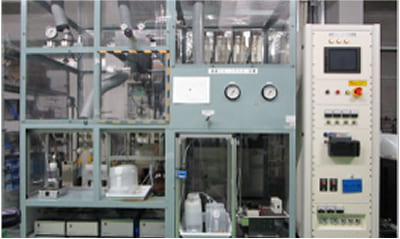
FQ(埋め込み)・TC開発
石英に直接熱電対を埋め込むことで、従来の製品よりも迅速な温度測定(応答性、感度向上)が可能になりました。また、小型化によって狭いスペースでも温度の測定が可能となりました。
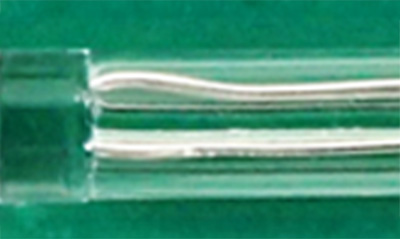
次世代半導体配線向け大型ルテニウムターゲットを開発、出荷開始
半導体分野においてスパッタリングターゲットは配線や電極用の非常に重要な材料として使用されます。当社は、高品質で高密度の大型ルテニウムターゲットを半導体向けの製品として開発に成功しました。
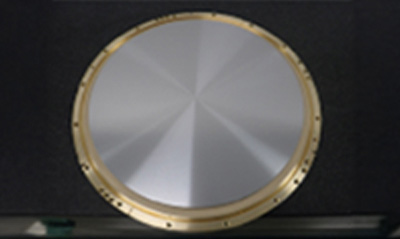
2020
株式会社Furuya Eco-Fronta Technologyを設立
Furuya Eco-Front Technologyは、FT-eco 触媒を活かした鮮度維持、防カビ、抗菌など環境製品の開発、製造、販売、輸出を事業としています。
2020年版経済産業省認定企業100選に認定グローバルニッチトップ
2014年に続き、2回連続の「グローバルニッチトップ企業100選」の認定となりました。前回認定を受けたイリジウムの加工技術を応用し新しい分野で高いシェアを有する部材の開発・提供や原材料のリサイクル、供給体制の整備を含めた活動が評価されました。
Anglo Platinum Marketing Limitedと株式会社Furuya Eco-Front Technologyの合弁契約締結
2021-第三ステージ 次なる飛躍へ、誰もやらない未来をつくる。
2023年、悲願の東証プライム市場上場を果たしました。時代の変化に伴うニーズを的確に捉え、最先端技術の研究開発に注力し、さらなる企業価値の向上を目指します。新たな市場開拓と事業の創造によって新たな価値を提供し、持続可能な未来への貢献を続けます。
2021
株式会社Furuya Eco-Front Technology上海を設立
EUVリソグラフィ向け高品位ルテニウム合金ターゲット開発
当社独自の溶解方法で含有不純物を極限まで低減する超高純度ターゲット製造技術を確立し、EUVリソグラフィ向け高品位ルテニウム合金ターゲットを開発しました。
EUVリソグラフィ(Extreme Ultraviolet Lithography、EUV露光)は極端紫外線を用いた半導体の製造技術で、半導体の微細化に欠かすことのできない技術です。
2022
東京証券取引所の市場区分の見直しにより、JASDAQ(スタンダード)市場からスタンダード市場に移行
AlScターゲット量産品として出荷開始
エレクトロ二クス産業が小型化と機能性を強化する中で、AlSc(アルミスカンジウム)合金は、優れた導電性と安定性を持った材料です。貴金属以外のスパッタリングターゲット量産品として新たなスタートをきりました。
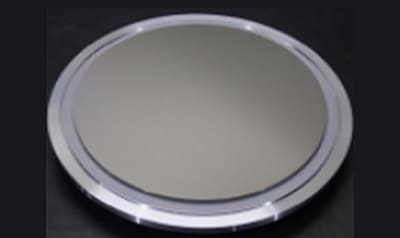
2023
東京証券取引所スタンダード市場から同取引所プライム市場へ市場区分を変更
12月にスタンダード市場からプライム市場へ移行し、よりパブリックな企業へと進化しました。
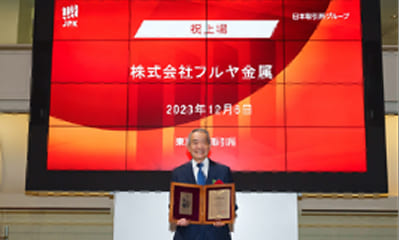
つくば工場C棟に石英加工ライン立ち上げ
半導体市場の拡大により半導体製造装置用石英部品の需要が高まる中、つくば工場に新たな石英加工ラインを設置し、生産体制を強化しました。これにより千歳工場、つくば工場の両工場での生産が可能となりました。千歳・つくばの2工場での生産を可能とすることにより、BCPを意識した体制が整いました。
2024
(株)ナノ・キューブ・ジャパン吸収合併
ナノ・キューブ・ジャパンは、マイクロ化学プロセスによるナノ粒子の製造、販売、受託開発を事業内容としている企業です。同社を吸収合併したことにより、ナノ合金の量産化技術開発が進捗しました。