Research and Development
Ir Fine Processing Technology
Distinctive features of Ir are that:
- It has a high melting point and excellent high temperature strength.
- Almost all high melting point metals are easily oxidized at high temperatures, while Ir has excellent oxidation resistance.
- High corrosion resistance (not affected by acid)
- Low electrical resistivity (approx. 5×10-8Ωm@20℃)
In addition, it has excellent properties such as low reactivity with carbon at high temperatures and the lowest oxygen permeability among metals, but it is not easy to perform plastic processing or machining.
We can apply Ir processing technology acquired over many years to detailed products.
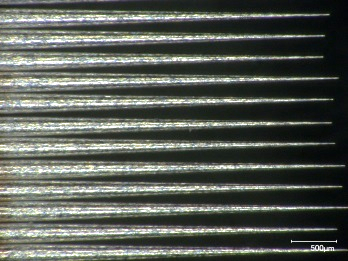
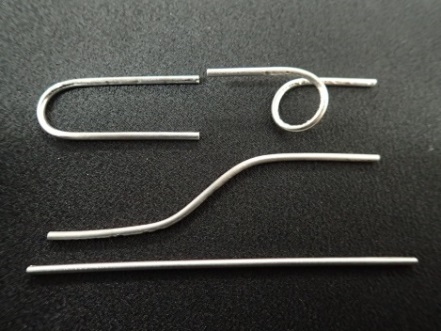
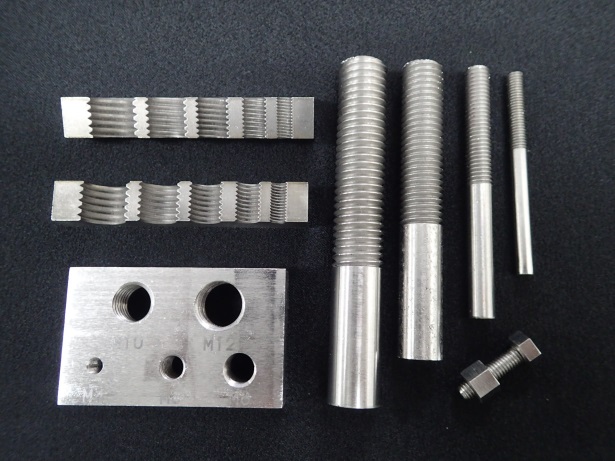
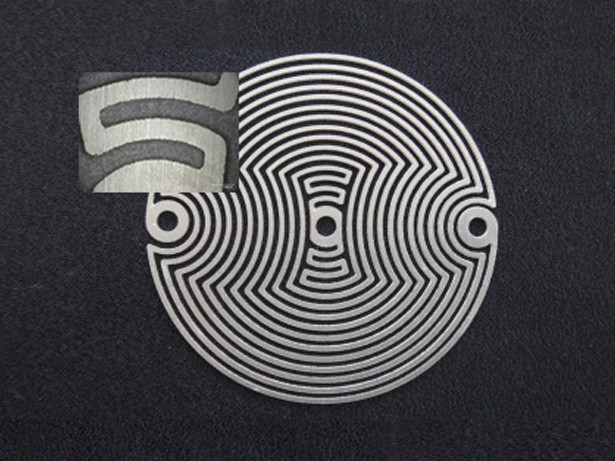
Product Examples
Wires, Tubes, Coils, Foil, Screws, etc.
Applications
Probe Pins, Various Types of Sensors, Thermocouple, Protective Tubes, Heaters, Medical materials, etc.
Ultra-high Purity Materials
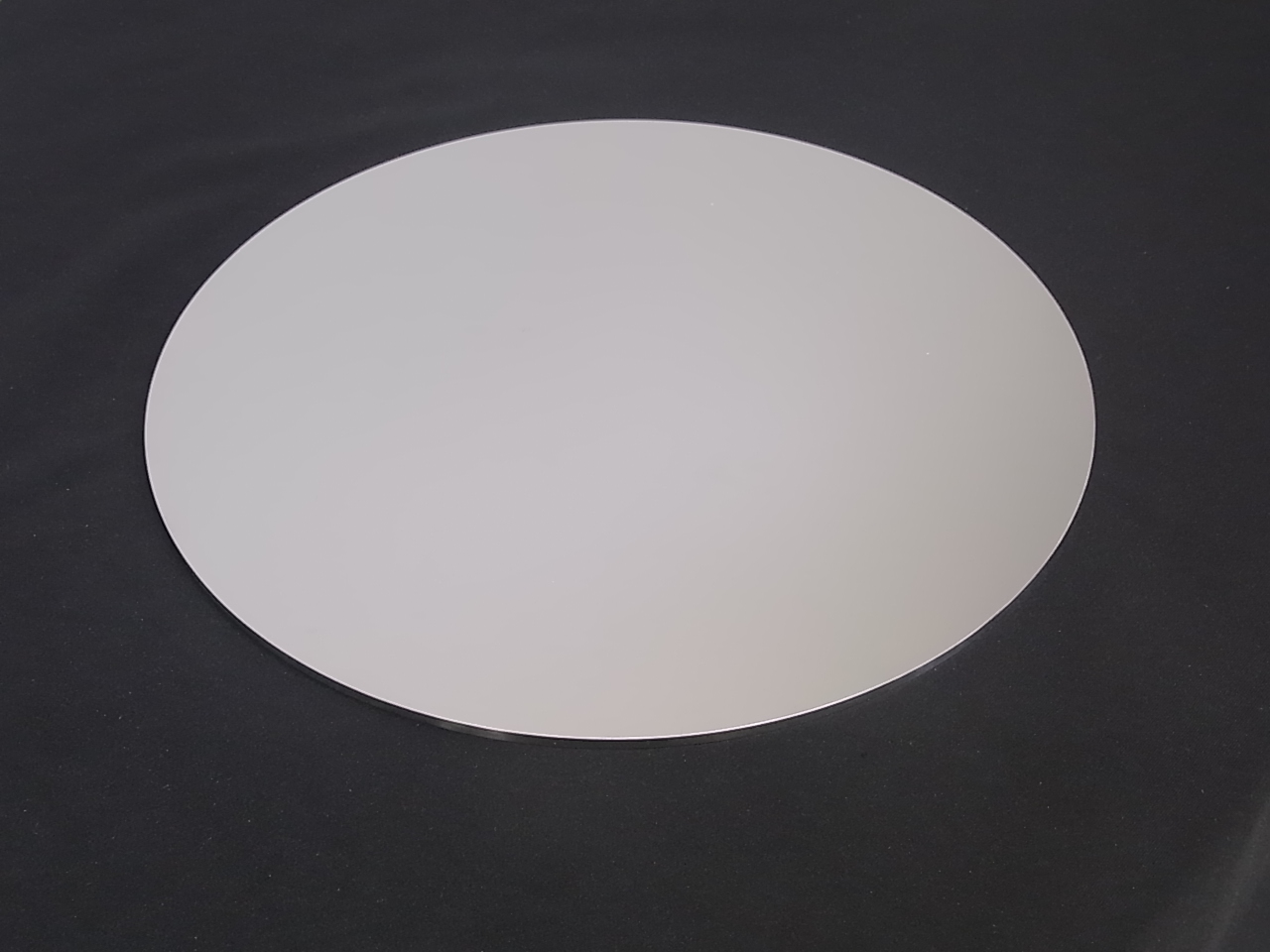
Furuya Metals has a variety of ultra-high-purity materials for making PGM thin films. Materials for semiconductors and materials for thin films are required to have low particle properties, low electrical resistivity, corrosion resistance, etc., and are required to have extremely high purity. Furuya Metals refines metals, particularly Ru and Ir, using our own refining processes to minimize metal impurities to 5N (99.999%) and 4N5 (99.995%) grade purity.
They are expected to be used in components for semiconductors requiring ultra-high purity, electrodes for next-generation memories typified by STT-MRAM, barrier films for next-generation LEDs, and MEMS electrodes. It is possible to flexibly cope with shapes and weights to meet customer demands, such as sputtering targets and shot shapes for PVD.
We are continuing development to meet increasingly complex and diverse needs, such as the development of PGM+X alloy materials.
AlSc and Al alloys for next-generation piezoelectric thin films
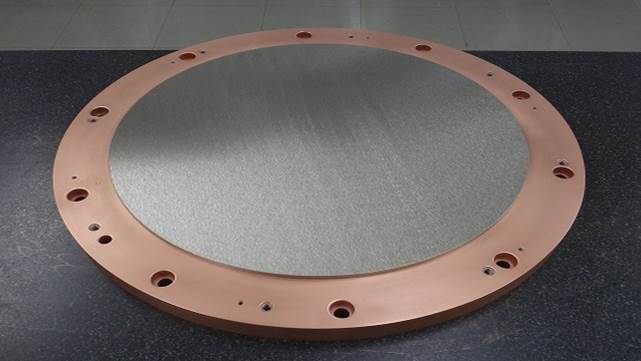
AlScN (aluminum-scandium nitride) is attracting attention as a next-generation piezoelectric thin film material. Changing the Al/Sc ratio changes its characteristics, and is expected to be applied to a wide range of applications, such as high-frequency noise filters for mobile phones and ultrasonic sensors for autonomous driving technology, etc.
Furuya Metals has long been developing AlSc sputtering targets by focusing on this combination of AlSc materials and Ru thin films (electrode materials). Furuya Metal's original powder fabrication and sintering technologies make it possible to provide large-diameter, high-density sputtering targets even in the Sc-rich compositional range, which has been considered difficult. In collaboration with research institutes and universities, we have also confirmed that a film using our target can provide sufficient characteristics as a piezoelectric element.
In order to meet the future needs of the market, we are developing not only AlSc alloy sputtering targets, but Al alloy sputtering targets as well, which use piezoelectric thin films.
Technological Development of FT-eco Catalysts
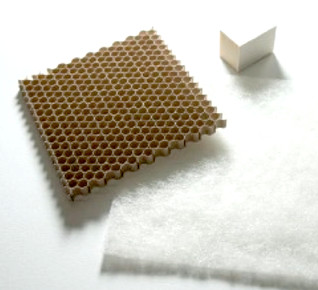
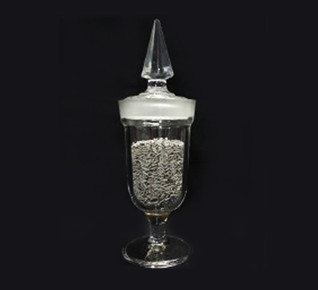
Catalysts are substances that work to promote specific chemical reactions, but many catalysts do not work unless they are in a high temperature environment, which is an issue for catalyst development.
Since 2015, Furuya Metal has been developing mass production technology for the "FT-eco Catalyst" that works at low temperatures, and has established mass production technology for various forms of it. This FT-eco catalyst has the function of efficiently decomposing and removing ethylene at a normal temperature, which accelerates the decay of fruits and vegetables, as well as VOCs (volatile organic compounds) that cause allergies and offensive odors.
In order to efficiently decompose and remove ethylene and VOCs with conventional catalysts, an environment of 200℃ or higher is required, but it is possible to efficiently remove these with FT-eco catalysts even in environments from below freezing to 30℃.
FT-eco catalysts are expected to be used in a wide range of situations, ranging from home appliances such as air conditioners, air purifiers, refrigerators, etc., to agricultural products, a wide range of storage containers for the food industry, and transport containers.
This FT-eco catalyst is a very interesting catalyst that will keep the developer interested, as the more one investigates, the more capabilities one can find.
We will continue to improve the FT-eco catalyst and aim to develop a catalyst that can be used in various fields.
Malodor Removal Data
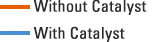
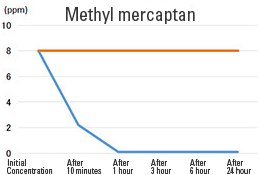
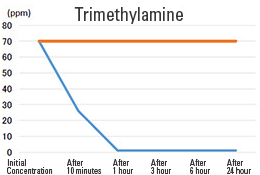
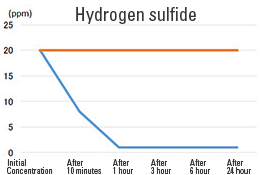
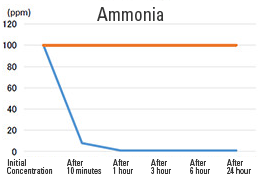
【Test Conditions】
Catalyst Weight (Pellet Type) |
1g |
---|---|
Reaction Volume | 9L |
Temperature | Room Temperature |
Measuring Equipment | Detector Tube |
【Test Consignee】
Japan Food Research Laboratories
Development of Mass Production Technology for Nano Alloy Based on Interelemental Fusion
“Interelemental fusion,” developed by Professor Hiroshi Kitagawa of Kyoto University, is a nano alloy synthesis technology that mixes elements at the atomic level that are said to be impossible to mix in the academic field of alloys.
For example, it has been found that when palladium (Pd) and ruthenium (Ru), which surround rhodium (Rh) on the periodic table, are mixed to create a PdRu nano alloy, it is identical to Rh in various physical properties, and has the same or higher catalytic performance.
In order to make various types of nano alloys synthesized by this innovative interelemental fusion technology widely available to the world, we are developing mass production technology with Professor Hiroshi Kitagawa of Kyoto University et al., at Furuya Metal.
Since the interelemental fusion technology is a synthesis method under a very demanding environment, establishment of mass production technology is a very difficult road.
However, since interelemental fusion technology is a technology that many companies are eagerly awaiting, we have been working on technology development every day so that we can soon satisfy everyone in these companies that have been waiting.
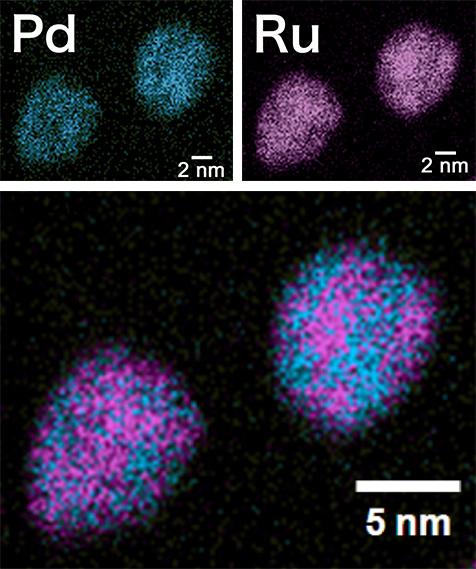
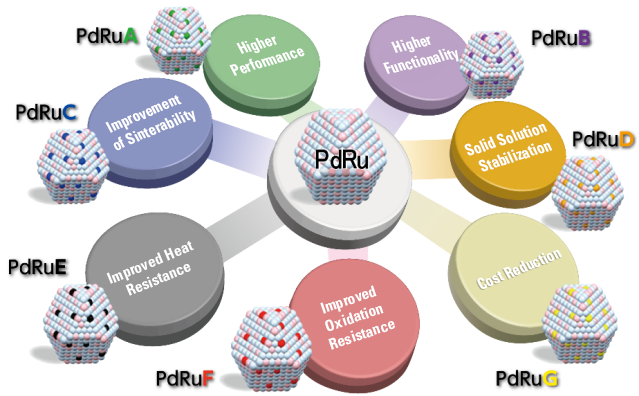